Editor's Note: The information in this blog is specific to Metrc in California. Individual states may have regulatory processes that differ with what is written in this article.
On a beautiful summer day, Heather logs into her computer, hoping to complete the final task of her workday: an R&D test. She accesses Package XXX05, creates a test sample, and transfers it to her lab.
The following morning, Heather is surprised to find her package's status has changed from "NotSubmitted" to "SubmittedForTesting." Puzzled, she wonders if this status is reserved for compliance testing.
Frustrated yet determined, Heather contacts the lab to explain the situation. It's then that she realizes her mistake: instead of adjusting the package for the R&D test, she had inadvertently created a compliance test sample. With a sigh, she accepts that she'll have to miss her planned dinner with friends to rectify the error.
Do you recognize the feeling? You’re not alone.
Mistakes like these are commonplace amongst cannabis operators, and although such errors happen frequently, preparation and knowledge can minimize how often they occur.
.png)
Frustrated with Constant Double Entry of Data in Metrc?
We hear you and we have the solution.
Staying compliant can be complicated enough, even without that constant double handling of data.
Take a look at this short clip — If it’s relatable to your daily workload, we can help!
Below is a list of 7 Metrc mistakes cannabis distributors can avoid. While this list is not exhaustive by any means, ensure that your team members are cognizant of these so that they do not need to miss their dinner plans with their friends!
1. Creating the Wrong Item Name / Category and Not Recognizing It
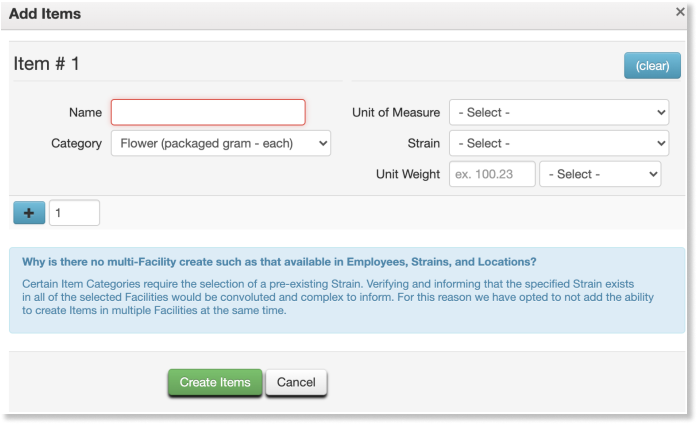
Let's talk about a common issue in the cannabis industry: creating items in Metrc. As a cannabis distributor, you're constantly adding new products to your inventory - from raw flower to finished goods. Metrc requires you to input details like the item name, unit of measure, category, and for flower products, the strain name.
Here's the problem: it's easy to make mistakes when creating these items. You might misname something, choose the wrong category, or mess up the unit of measure. While you can fix these errors if you catch them early, once an item is in use, you're stuck with it. Your only option then is to create a new, correct item from scratch.
This becomes a real headache when item names are too similar or just plain wrong. Imagine trying to repackage products when you can't tell the difference between two similarly named strains. It's a recipe for inventory chaos.
The key is to be consistent and clear when naming items in Metrc. Use a system that everyone on your team understands and follows. Double-check your work before saving, and make sure each item name is distinct enough to avoid confusion.
By being careful with how you create and name items in Metrc, you can save yourself a lot of trouble down the line. It might seem like a small thing, but in the world of cannabis compliance, these details really matter.
2. The Tag Crisis: Overlooking Metrc Package Tag Orders
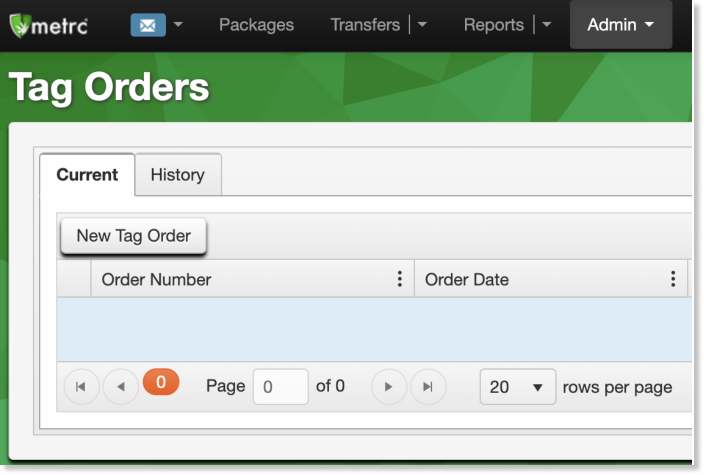
One of the biggest blunders in Metrc management is forgetting to order package tags. These small identifiers are the lifeblood of your cannabis tracking system, and running out can bring your entire operation to a screeching halt.
Here's why this mistake is so critical:
- Limited Ordering: In Metrc, you can only order one set of tags at a time through the Admin section. You must wait for your current order to arrive and be received before placing the next one.
- Delivery Delays: While delivery times have improved, it can still take 1-2 weeks for tags to arrive. This delay can be catastrophic if you've run out.
- Tag Limits: Each licensee has a maximum number of tags they can order per set, visible in Metrc during ordering. This limit means you can't simply bulk order to avoid the issue.
- Activation Required: Once tags arrive, you must mark them as received in Metrc before use. Forgetting this step can lead to further delays.
- No Early Order Restrictions: Metrc doesn't limit how early you can order tags. Despite this, many operators wait until the last minute, risking operational downtime.
The Consequence: Running out of Metrc tags can paralyze your cannabis business. Without tags, you can't create new packages, transfer products, or maintain compliance with state regulations.
.png)
Tag Management 101: Keeping Your Metrc Pipeline Flowing
Don't let tag shortages catch you off guard. Follow these simple steps to stay ahead of the game:
- Tag Inventory Checks: Make it a habit • Schedule weekly tag counts • Keep a running tally of tags used vs. tags on hand
- Proactive Ordering: Stay ahead of the curve • Place new orders when you're down to your last month's supply • Don't wait until you're scraping the bottom of the barrel
- Calendar is King: Let technology be your reminder• Set up recurring calendar alerts for tag inventory checks• Add reminders for placing new orders based on your usage patterns
- Team Effort: Spread the knowledge• Train multiple team members on the tag ordering process• Create a clear SOP for tag management and ordering
- Buffer Stock: Always have a safety net• Maintain a small emergency supply of tags• Adjust your "reorder point" based on your operation's growth
By implementing these strategies, you'll transform tag management from a potential crisis point into a smooth, routine part of your operations. Remember, in the world of Metrc compliance, an ounce of prevention is worth a pound of cure!
Streamlining Tag Management with Distru
While manual processes can help, integrating Distru with Metrc can revolutionize your tag management. Distru offers a real-time, two-way sync with Metrc, ensuring your inventory is always up-to-date. This integration not only helps prevent tag shortages but also streamlines your entire compliance workflow. With Distru, you can continue operations even during Metrc outages, expedite package assignments, and manage all your COAs, test results, and manifests in one place. Plus, our expert cannabis industry support team is always ready to assist, usually within 5 minutes. By leveraging Distru's cannabis-specific workflows and Metrc integration, you can say goodbye to repetitive data entry and the stress of tag management, keeping your operation smooth and compliant.
Remember, in the world of cannabis compliance, running out of Metrc tags is like a retailer running out of price tags - it brings everything to a standstill. By staying proactive and utilizing Distru, you can avoid this common mistake and keep your operation running efficiently and compliantly.
3. The Void Trap: Metrc's Post-Departure Transfer Dilemma

Metrc allows licensees to create transfers up to 24 hours before departure, with most opting to do so the night before or morning of delivery. While the system provides an option to void transfers, this feature becomes problematic once a transfer has departed. Voiding a transfer after departure not only returns all associated packages to the originator's inventory in Metrc but also violates BCC regulation section 5314, which explicitly prohibits changing a shipping manifest post-departure.
When faced with a canceled delivery, the best practice is to have the driver complete the journey to the receiving licensee and request them to 'reject' the transfer upon arrival. This approach ensures compliance with regulations requiring drivers to follow specified routes without detours. It also prevents the mismatch between physical and recorded package locations that occurs when voiding mid-journey.
For those using the Transfers Hub, it's worth noting that transporters cannot alter or void transfers after departure. The 'Depart' button automatically records the actual departure time, adding an extra layer of compliance. By adhering to these guidelines, cannabis distributors can navigate the complexities of Metrc transfers while maintaining regulatory compliance, ensuring smooth operations in this highly scrutinized industry.
.png)
4. The Premature Reception: Metrc's Inventory Integrity Risk

The transfer functionality in Metrc is crucial for tracking cannabis movement between licensees. When receiving an incoming transfer, it's vital to physically verify that the packages match the manifest before marking them as received in Metrc. This process also applies to rejected transfers, where the originating licensee must confirm the returned items in the Transfers > Rejected section after the driver brings them back.
There's often pressure to quickly make incoming inventory available for sales, but rushing this process can lead to significant problems. Marking a transfer as received in Metrc before physically verifying the goods creates a mismatch between your digital and physical inventory. This discrepancy not only affects your internal operations but also puts you at risk during audits and inspections.
Remember, accepting inventory in Metrc makes you liable for those goods. If items are misplaced during transport or there's a quantity discrepancy, you'll be responsible for inventory you may not actually possess. Always prioritize accuracy over speed when receiving transfers. Take the time to thoroughly check each package, ensuring your Metrc inventory precisely reflects your physical stock. This diligence maintains the integrity of your cannabis inventory management and keeps you compliant with regulatory requirements.
5. Creating a Production Batch from An Already Tested Package
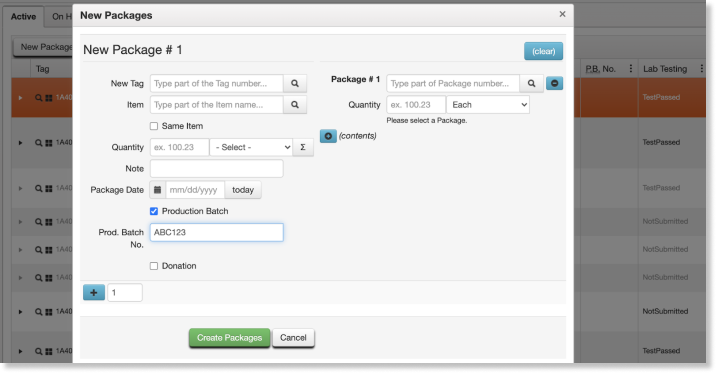
In Metrc, Distributors and Microbusinesses can create sample packages for testing using the 'Submit For Testing' button. Once tested, labs update the source package's status directly in Metrc. Subsequent packages created from these tested sources typically inherit the test results, maintaining the chain of compliance.
However, a common mistake occurs when creating new packages from already tested sources. If the 'Production Batch' box is checked during this process, it resets the package's test results to 'NotSubmitted'. This feature is intended for new concentrates, infused edibles, or infused non-edibles at the point of production, not for repackaging already tested products.
.png)
While this error isn't irreversible – you can discontinue the package and recreate it – it's an unnecessary complication that can disrupt your workflow and potentially cause compliance issues. Remember, you can't mark an existing package as a Production Batch; this designation is only available during package creation. By being mindful of this checkbox, you can ensure your Metrc inventory accurately reflects your products' testing status, streamlining your operations and maintaining regulatory compliance.
6. The Discontinue vs. Adjust Dilemma: Preserving Metrc Accuracy

Metrc provides the option to discontinue packages created from existing ones, a function accessible only within Metrc itself, not via API. This feature is crucial when correcting errors such as selecting the wrong Metrc item during package creation. Users can change the item within 24 hours of creation using the 'Changing Item' option; beyond this window, discontinuation becomes the only recourse. However, some states might allow corrections within Metrc for a limited time beyond 24 hours. It's essential to check your state's specific guidelines.
When faced with quantity errors in newly created packages, the best practice is to discontinue rather than adjust, even though adjustment is possible. Adjustment reasons, defined by the State of California, include options like display sample usage and R&D testing. While 'incorrect quantity' is an available reason, it's intended for transfer-related discrepancies, not package creation errors. It's important to note that available adjustment reasons might vary by state. Consulting your state's Metrc guidance for the most up-to-date list and their intended purposes is recommended.
Importantly, adjustments exceeding 3% can trigger government alarms, potentially leading to increased scrutiny. Therefore, it's advisable to use adjustments sparingly and opt for discontinuation when correcting package creation errors. This approach maintains the integrity of your Metrc inventory, ensures accurate tracking, and minimizes the risk of regulatory red flags. Remember, in Metrc management, precision in your actions is key to maintaining compliance and operational efficiency, and staying informed about your state's specific requirements is crucial.
7. The R&D Testing Trap: Avoiding Unintended Compliance Triggers
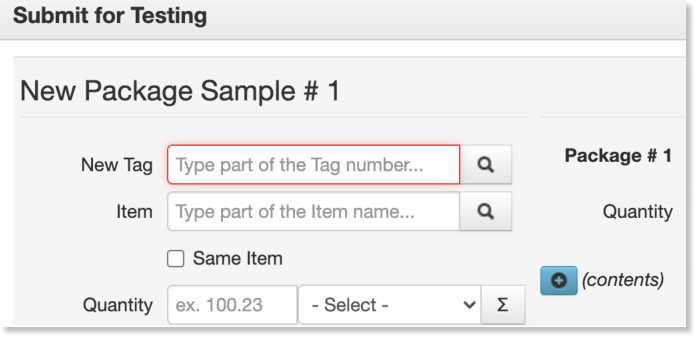
In Metrc, the distinction between compliance testing and R&D testing is crucial, yet often misunderstood. This misunderstanding can lead to unnecessary complications and potential compliance issues. Here's what you need to know:
Compliance Testing:
- Use the 'Create Test Samples' feature for compliance testing of bulk flower or retail-ready finished goods.
- These samples are created and transferred to labs through an outgoing transfer in Metrc.
- This process is designed specifically for mandatory compliance testing.
R&D Testing:
- R&D tests are separate from compliance tests and require a different approach in Metrc.
- Creating a test sample or transferring any package to a lab for R&D purposes inadvertently triggers the compliance test flow.
- This unintended action forces the lab to conduct a full compliance test and update the package's testing status in Metrc.
The Correct Approach for R&D Testing:
- Use the 'adjustments' feature in Metrc.
- Select 'Research and Development' as the reason for adjustment.
- Adjust the quantity of the package you wish to R&D test.
- Physically provide the sample to the lab without creating a Metrc transfer.
By following this procedure, you maintain accurate inventory tracking while avoiding the unintended consequences of initiating a compliance test. Remember, in the world of cannabis compliance, distinguishing between R&D and compliance testing in Metrc is not just a technicality—it's a critical aspect of maintaining regulatory alignment and operational efficiency.
.png)
Streamlining Metrc Compliance: Why Distru is the Ultimate Solution for Cannabis Distributors
While understanding and avoiding common Metrc mistakes is crucial, cannabis distributors can take their operations to the next level with Distru. Here's why Distru stands out as the premier choice:
- Real-time Metrc Sync: Distru offers a seamless, two-way sync with Metrc, ensuring your inventory is always up-to-date across both platforms. This real-time integration minimizes discrepancies and reduces the risk of compliance errors.
- Cannabis-Specific Workflows: Built with true industry knowledge, Distru streamlines your compliance and reporting workflows. Say goodbye to repetitive data entry and Metrc loading spinners, and hello to efficiency.
- Unparalleled Support: Distru's support team is not just responsive – they're experts in both the platform and cannabis compliance. Get your questions answered and problems solved, usually within 5 minutes or less.
- Operational Continuity: Even when Metrc experiences downtime, Distru keeps you operational. Continue working within Distru, and your data will sync once Metrc is back online, ensuring uninterrupted business operations.
- Advanced Features:
- Expedited Package Assignment: Accelerate fulfillment with in-line repackaging, allowing you to split Metrc packages directly within order forms.
- Document Management: Efficiently manage COAs, test results, and manifests all in one place, saving hours of manual document handling.
- Error Prevention: Many of the common Metrc mistakes discussed in this article can be mitigated or entirely prevented through Distru's intuitive interface and built-in safeguards.
- Scalability: As your cannabis distribution business grows, Distru grows with you, offering robust solutions that adapt to your increasing complexity and volume.
By choosing Distru, cannabis distributors not only solve the common Metrc pitfalls but also gain a comprehensive tool that enhances overall operational efficiency, ensures stricter compliance, and provides a competitive edge in the fast-paced cannabis market. With Distru, you're not just managing Metrc – you're optimizing your entire distribution process.
Schedule a Demo: Take the first step towards optimizing your cannabis distribution business. Our team of experts is ready to show you how Distru can streamline your operations, ensure compliance, and boost your bottom line.